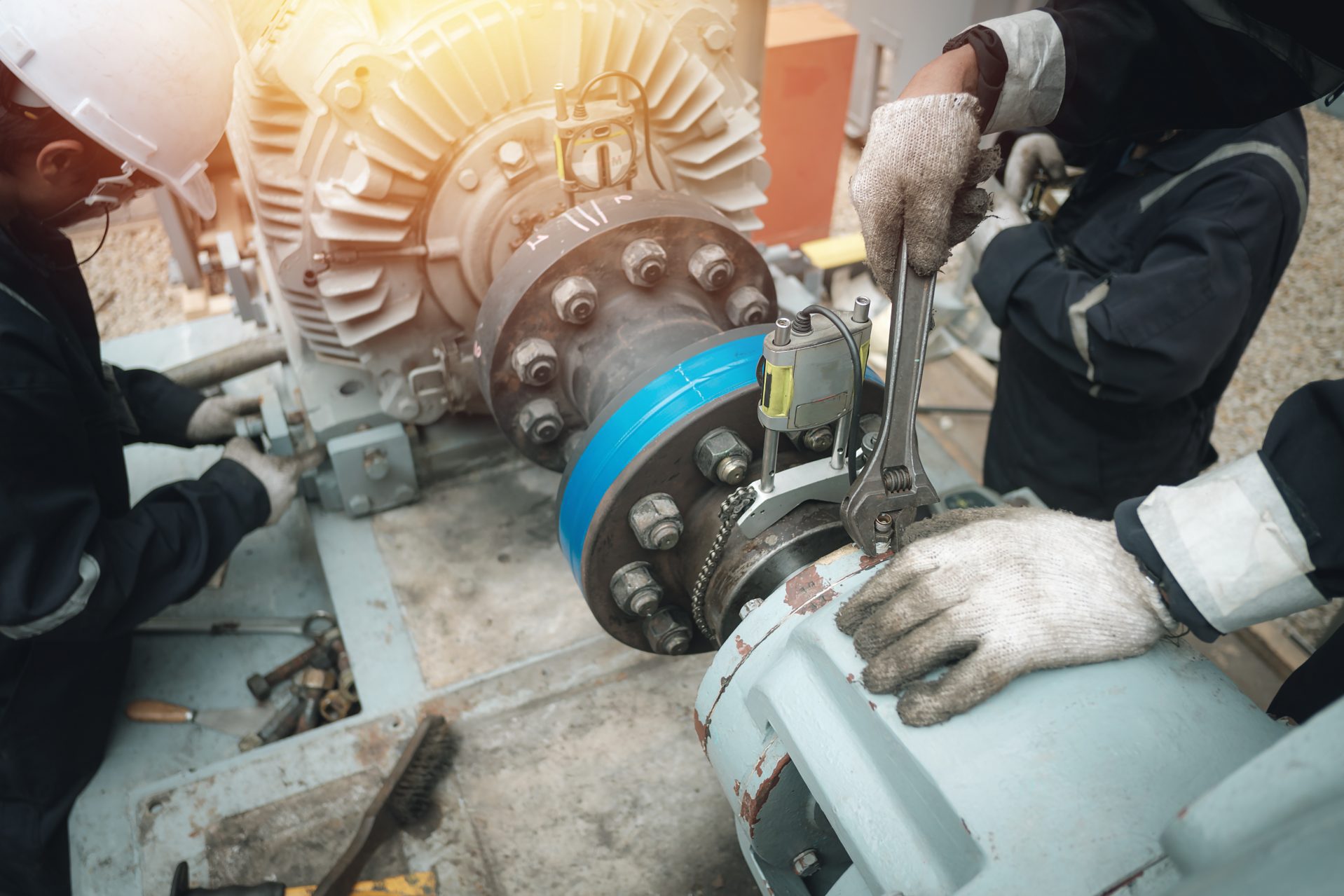
Maintenance
Remove The Root Cause of Failure And Minimize Maintenance
Maintaince-Free Solution for Uninterrupted Operations
At Zytec, we understand the challenges faced by industries when it comes to maintenance costs and downtime. Traditional couplings require frequent lubrication and upkeep, leading to significant expenses and productivity losses. With our non-contact drives, you can bid farewell to these concerns. By eliminating the need for physical contact, our magnetic couplings offer a maintenance-free solution, reducing downtime and boosting operational efficiency. Say goodbye to costly repairs and hello to uninterrupted productivity.
Reduce overall vibration by up to 80%
Non-contact drive means that there is no physical contact between the motor and the load, e.g. pump, fan. This simple fact reduces vibrations in your rotating equipment by up to 80%.
This results in:
- Operational misalignment becomes irrelevant. Unavoidable temperature variations due to summer/winter, day/night, process stop mode (cold)/operational mode (hot) cause misalignment. The non-contact drive eliminates the cause of these operational misalignment failures.
- Laser alignment is no longer required. Laser alignment and positioning of the motor base is prone to human error and time-consuming. The non-contact drive requires only visual positioning of the air gap without laser alignment equipment.
- No forces through the shafts in your drive line from the motor to the rest of the system or from the system to the motor.
- Longer life for all components in your system
Extend the life of many components and easily extend maintenance intervals by up to 4-10 times
The non-contact drive is a mechanical variable speed drive. It is used in circumstances where a production process needs to be controlled at its best efficiency point. This reduces pressures, forces and stress in your installation, which increases the life of many components.
The contactless drive is also a torque limiter. This can be used in situations where a motor with a heavy load (high inertia) needs to be started, such as fans. It always operates as a mechanical soft starter by nature.
This results in a multiple increase in lifetime of:
- Bearings of your motor, pump, fan, generator, compressor, etc. due to reduced shaft loads and no fluting
- Pump seal due to reduced vibration and no cavitation
- Pump impeller and housing due to elimination of cavitation
- Electric motors due to the use of a mechanical variable speed drive without harmonics
- Choke valves due to elimination of cavitation and reduced pressures
- Piping by eliminating cavitation and reducing leakage
This results in:
- Elimination or reduction of spare parts and inventory
- Increased production uptime
- Reduced Total Cost of Ownership (TCO)
- Reduced preventive (visual) inspections as a precautionary measure
Reduce human error
Multifunctional non-contact magnetic drives are easy to install. Compared to the installation of “contact” couplings (claw couplings, tire couplings, fluid couplings, etc.) or Variable Frequency Drives (VFDs), the chance of human error is significantly reduced. Fewer installation steps are required. Also, the simple fact that maintenance is much fewer means, by definition, a reduction in human error.
This results in:
- Eliminate the risk of human error by aligning a motor with a pump, fan, compressor or generator. Heavy motors weighing more than 100 kg are difficult to maneuver. The results of how well the alignment is done depends on the time spent by the mechanic.
- Much less human error due to the extended life of many components.
- Less maintenance simply means less human error in all processes related to a maintenance job. This includes parts not being available when needed, wrong parts not being fitted, parts not being fitted correctly, bolts not being tightened, etc., etc.
- Easy to train mechanics in just one day. Reducing reliance on highly skilled technicians.
- Robust rotating equipment
– Not sensitive to dirt or wet environments
– Significantly reduced collateral damage to the drive line if something unexpected happens.
– Increased equipment availability - Reduced downtime
- Reduced hand-on tool time
- Increased Overall Equipment Effectiveness (OEE)
Download the whitepaper ‘Eliminate the root cause of failure’
↓
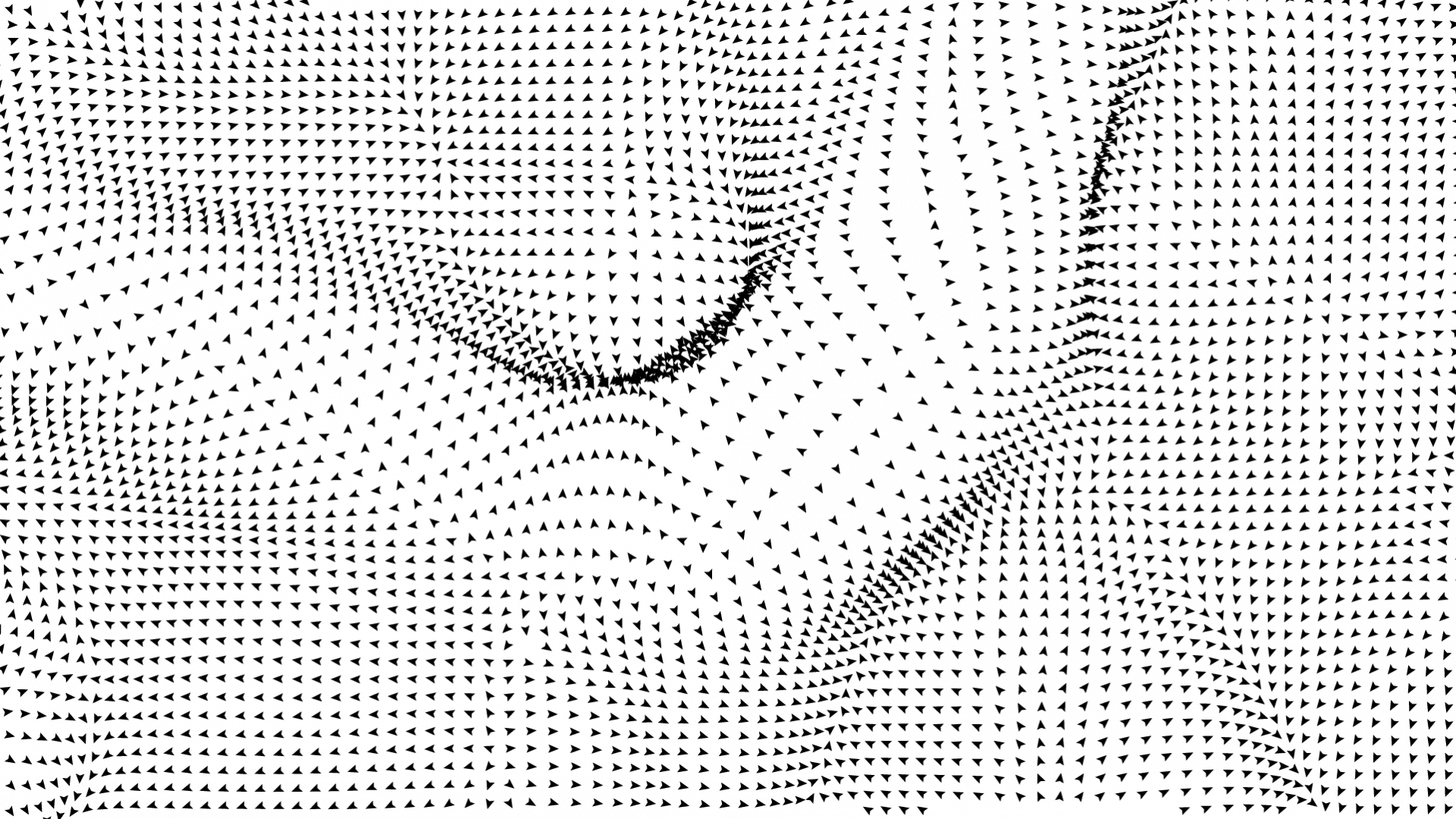
Whitepaper
Download
"*" indicates required fields