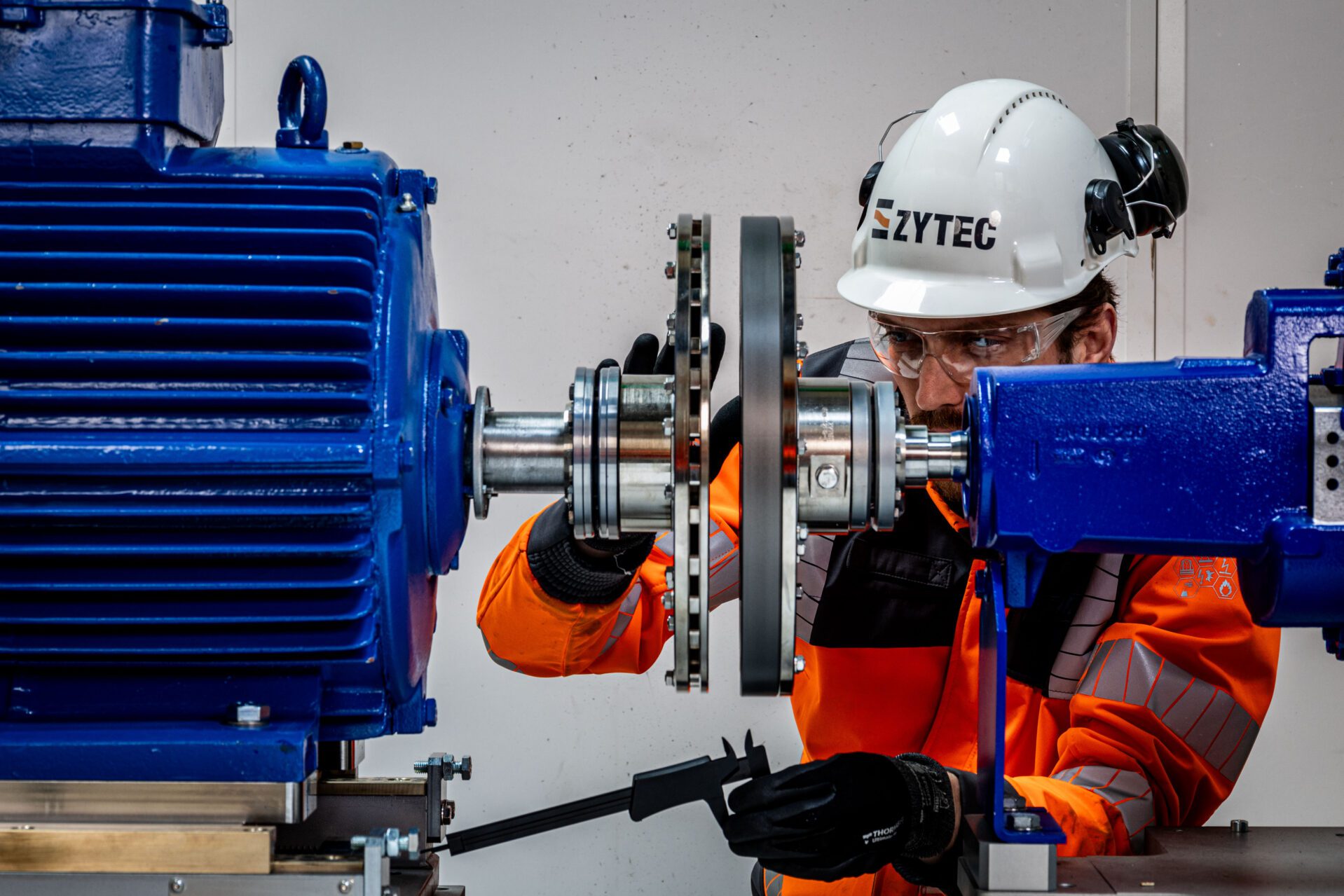
Accelerated Progress Towards Climate Goals
Zytec mechanical speed control on large pumps
Source: Financieel Dagblad Friday September 15th, 2023, number 218
Of all the electrical energy used in the industry, 65% is consumed by rotating equipment such as pumps, fans, and compressors. In the Dutch industrial sector, there are more than 100,000 pumps with a power rating exceeding 30 kW. All of these pumps are oversized during the design process, presenting a massive potential for energy and CO2 savings, yet this potential remains largely untapped.
How is this possible? Business Development Director Danny van Nielen of Zytec in Nieuwegein explains. He advocates for the inclusion of a measure called ‘Speed Control on Pumps above 30 kW’ in the national energy-saving agenda. The estimated savings, assuming average and conservative assumptions in the calculations, would amount to 3.8 TWh and 1.0 million tons of CO2 by 2030.
Most Dutch process technology factories were built after World War II when energy consumption was not a priority. Pumps account for 20% of the total electricity consumption in the industry, with the process industry ranging from 25% to 50%.
Oversizing
Many pump installations are intentionally oversized as a precaution to mitigate risks such as wear and tear, pipe clogging, and the temperature effects of the medium. The Fraunhofer Institute estimated in 2005 that 75% of industrial pumps (worldwide) were oversized by at least 20%. This excess capacity is either controlled by throttling valves/regulating valves behind the pump or continuously circulated. Van Nielen says, “This is pure energy wastage.”
Fortunately, existing excess capacity can be addressed through retrofitting. “The food and pharmaceutical industries are already doing this, primarily using lower-power pumps. Electronic speed controllers (frequency converters) regulate the pump motor based on the production process’s needs,” says Van Nielen. “For high-power pumps above 30 kW in the process industry, these electronic speed controllers are often complex, difficult to install, and economically unviable. In explosive (ATEX) environments, such electronics are not desirable.”
Non-Contact
A mechanical speed controller like the one from Zytec becomes profitable in less than two years. This is because it saves on energy costs, maintenance, and downtime. Installation is straightforward and can be done in ATEX environments as well. The magnetic coupling operates without physical contact between the electric motor and the pump. Van Nielen explains, “During operation, misalignment always occurs between the motor and pump shafts due to temperature variations, structural stiffness, and hydraulic pressure waves. This causes vibration in a conventional, fixed coupling. A contactless magnetic coupling reduces vibrations and renders misalignment irrelevant during operation. This significantly extends the maintenance interval for bearings and seals.”
The pump flow rate is controlled by adjusting the air gap between the two discs of the magnetic coupling. A larger air gap results in a lower speed. This allows the pump capacity to be adjusted to match the production process. “This leads to energy savings of 30% to 50%. This unnecessarily wasted energy doesn’t need to be sustainably generated and helps alleviate the critical grid congestion.”
Reduced Maintenance
Van Nielen adds, “The maintenance interval is extended three to twelve times. No maintenance means no downtime and, therefore, no production loss. The longer lifespan of the electric motor, pump, coupling, and piping results in a lower carbon footprint. It reduces the pressure on the need for technical maintenance personnel, who are currently difficult to find.”
TCO vs. CAPEX
So, why isn’t the Dutch process industry lining up for contactless couplings on a large scale? Van Nielen explains, “They remain unknown, despite their use by companies like Tata Steel, BASF, Air Liquide, Vitol, Sabic, and Waterschappen. Even within these large companies, communication and decision-making are slow.”
The system in companies where budgets are allocated hinders the rapid implementation of innovation. These magnetic couplings have the lowest Total Cost of Ownership (TCO), but procurement only looks at the initial investment (Capital expenditure, CAPEX). Companies allocate their CAPEX to departments, and there is always too little, often already allocated to other projects. Introducing a new project creates decision-making stress. A small-scale magnetic coupling project falls to the bottom of the pile.
Van Nielen concludes, “Once the CAPEX budget cap is reached, there is no room left for magnetic couplings, even though they save much more on energy and maintenance. The maintenance department appreciates the reduced maintenance intensity but doesn’t see any of the energy savings reflected in their budgets. The solution is for us to conduct a quick scan of all pumps, bundle them into a business case, and roll them out in phases.”
Advocacy
Van Nielen advocates for the implementation of a measure called ‘speed control on pumps above 30 kW.’ “Let’s conduct an inventory of all pumps larger than 30 kW, bundle eligible applications, and implement them in phases. With 3.8 TWh and 1.0 million tons of CO2 savings, this subject deserves a place on the energy-saving agenda. It’s a concrete, straightforward project that can significantly contribute to achieving the industry’s climate goals by 2030.”Zytec mechanical speed control on large pumps
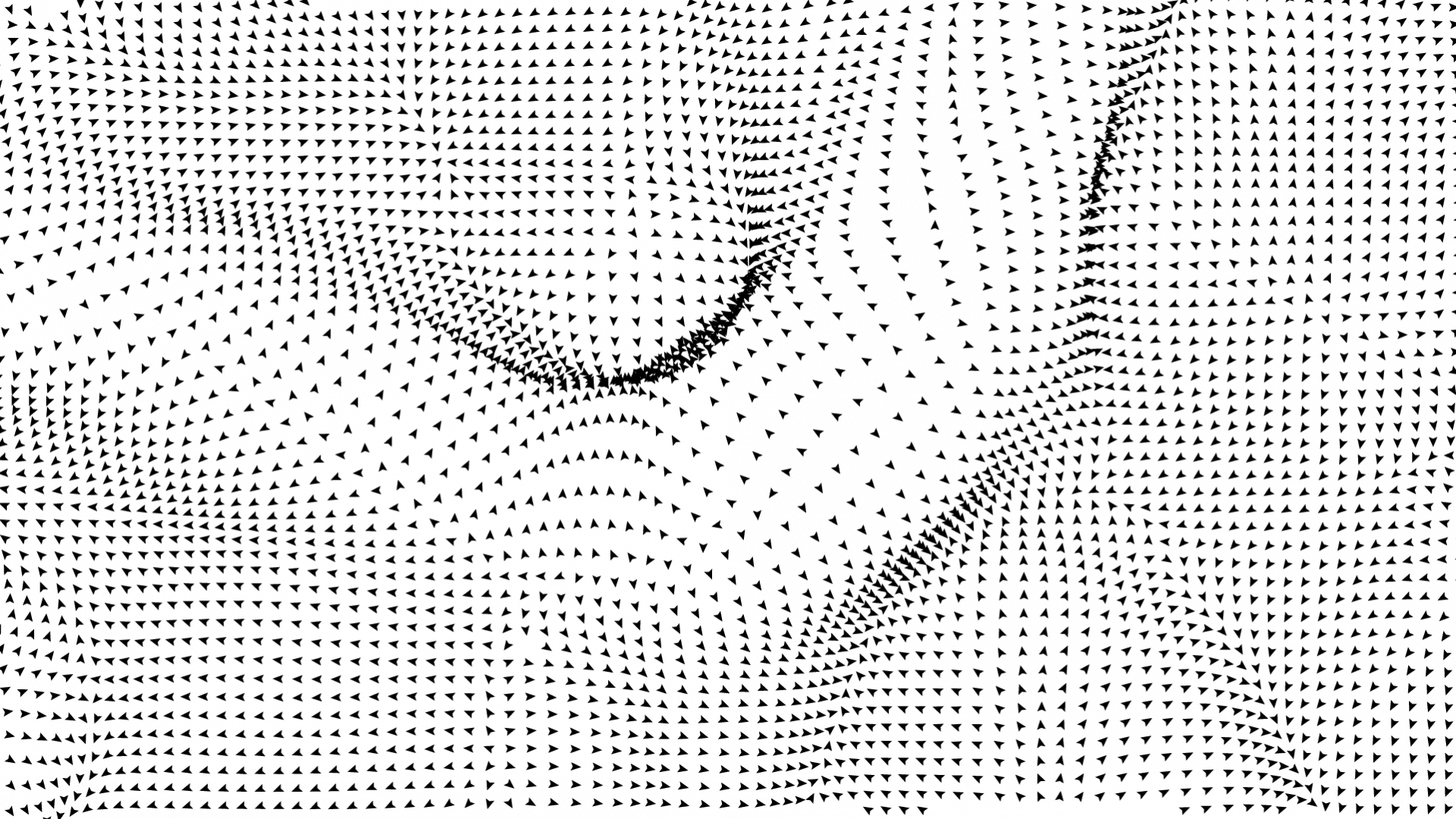