
ZYTEC’s Non-Contact Drives at Tata Steel
A success story of eight years maintenance-free operation
Tata Steel and Non-Contact Drives: A success story of eight years maintenance-free operation
The challenge: reduce maintenance, energy consumption, and costs.
At Tata Steel, one of the most CO2 efficient producer of steel products in the world, innovation and efficiency are very important. In Cold Rolling Mill no. 22, steel coils are rolled to a thinner gauge, a process that generates significant amounts of heat. This heat is dissipated using a special rolling fluid that is continuously pumped through the plant. Before 2016, these pump installations suffered from leaking seals, damaged bearings, and excessive electricity consumption. The traditional pump system often led to production downtime.
Goal:
Tata Steel faced the challenge of:
- Reducing pump maintenance.
- Significantly lowering energy consumption.
- Improving system reliability without extensive downtime or major investments in complex systems.
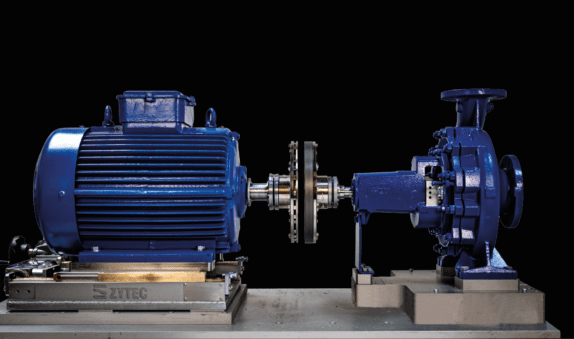
The Choice for Non-Contact Drives
In 2016, Tata Steel introduced Zytec’s Non-Contact Drives (NCD) as an innovative solution. Within just two days, four of the eight pumps were equipped with these advanced magnetic couplings. The quick installation of the NCDs was possible without requiring modifications to the existing infrastructure. The combination of easy installation, high electricity savings, increased productivity, reduced maintenance intervals, and lower costs made this technology an obvious choice for Tata Steel.
Eight Years Later: 2024
After eight years, the pumps in cold rolling mill no. 22 are still running. This has resulted in a long-term, low-maintenance operation with impressive outcomes:
Energy savings: Over 1 million kWh is saved annually, which in 2024 is equivalent to the energy consumption of 415 households.
No maintenance: Since installation, there have been no leaks, failures, or need for further maintenance. The redundant backup pumps are no longer needed, because a single set has proven sufficiently reliable.
Cost reduction: No more production losses due to failures, significantly lower material costs, and reduced labor requirements for repairs. Less cost for electricity
Environmental benefits: Thanks to reduced energy consumption and the elimination of maintenance, the ecological footprint of Cold Rolling Mill No. 22 has been significantly reduced.
Conclusion: Innovation with impact
The choice for NCDs demonstrates how a seemingly small adjustment can have a major impact. The rapid implementation and proven durability make it a prime example of cost-effective and future-proof production. Thanks to this technology, the pumps continue to operate effortlessly—already for eight years without maintenance—while significantly reducing both energy consumption and costs. What once started as a challenge has turned into an inspiring success story for all industries.
Advantages of Non-Contact Drives
What makes NCDs so special?
- Reduced maintenance: The contactless magnetic operation eliminates seal leaks and bearing damage, drastically reducing maintenance requirements.
- Energy efficiency: Traditional throttle valves can remain open, achieving up to 50% electricity savings.
- Increased productivity: Less downtime leads to higher uptime.
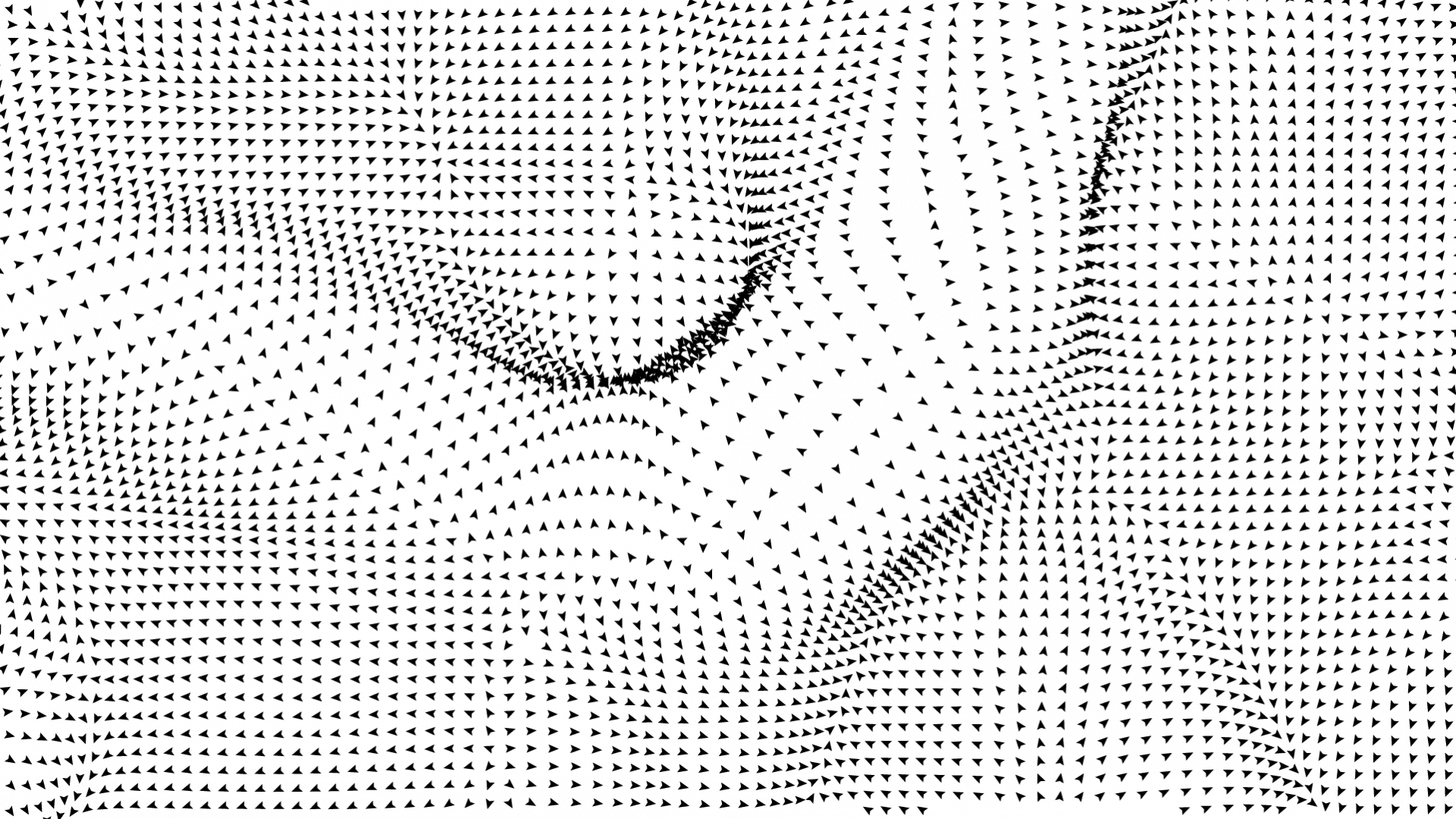
10 February 2025